Our results show that service quality is indeed part of most of the configurations that lead to performance, but there are other ways as well. It is quite interesting that internal service involvement is part of all configurations that lead consistently to performance. This is remarkable as this dimension of industrial service excellence is a special challenge for manufacturing companies.

In retail, you typically ask things about staff product knowledge (think Adidas and knowing what type of running shoe best suits your use) and recommendations. You can also assess merchandise knowledge (what goes with what), friendliness, and availability (were team members on the shop floor easy to engage). Service quality is especially important in automotive because the customer’s car must be fixed and completed on time.
Your toolkit for driving manufacturing excellence
It is also important to evaluate customer demands to ensure that your organization is only meeting those demands and not creating more than what is necessary. High quality can only be achieved once every part of the process is done correctly. It can be helpful to organize work areas in a way that will allow potential problems to become visible right away. When a mistake does occur, stop working immediately to correct the mistake before continuing. By systematically exploring new ideas you can encourage employees to do the same without fear of failure. Sometimes it can occur through a major initiative or total upheaval within the business.
With Hiver, they were able to streamline communication and workflows, keep track of critical customer and project-related information, and most importantly, have access to real-time customer service metrics. Only employees with the knowledge and opportunity to be successful decision-makers can pave the way for future business success. By empowering employees and giving them the tools they need to be successful, businesses can ensure that they have a solid foundation to build continued manufacturing excellence. The manufacturing process is constantly evolving, and to maintain a competitive edge, businesses must continually strive for manufacturing excellence. Standard cost, complexity reduction, and maintaining a valued and credible performance system are all essential components of manufacturing excellence. And, as any business leader knows, these components are all driven by the common denominator of knowledge-driven involvement.
The Importance of Continuous Improvement
Then, outline what it is you want to achieve – both with broad goals and specific KPIs that will measure your success. For example, if you’re looking to cut waste in your factory, you might go with Lean Management. If you’re looking to enhance the customer experience, you might consider Six Sigma. When you’re ready to put your operational excellence plan into place, consider these five operations best practices.
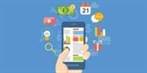
However, if your company provides excellent customer service, 78% of consumers would do business with a company again after a mistake. Ultimately, operational excellence is not just about reducing costs or increasing productivity in the workplace. It’s about creating the company culture that will allow you to produce valuable products and services for your customers and achieve long-term sustainable growth.
Statistical Process Control (SPC)
Configuration one is the empirically most important one and needs conditions two to six to be present and is valid only in companies where services are important. The effort reduced deaths by 10 percent, virtually eliminated bloodstream infections in participating hospitals, and saved billions of dollars in the costs of treating infections. The safety checklist is a prime example of the process standardization that lies at the heart of operational excellence. Having a very flat organizational structure without a production control department is part of what makes Hypertherm extraordinarily efficient, Duggan says.
- If the intrinsic needs of the customer is a mix, there is a quality gap if any of the quality indicators differs from that mix.
- It's undeniable that a well-trained, positive customer service team can make your company the best version of itself.
- These metrics are indicators of cost efficiency and high productivity, respectively.
- It is essential to realize that past leadership decision-making has created and supported most organizational costs.
- While the two terms sound very similar, functional excellence describes when a company’s support functions (such as finance or legal) perform in a superior way that helps the business excel.
Success leads to not only great customer service, but also increased employee satisfaction. It’s also the best available way to understand customer sentiment and whether or not your efforts are paying dividends. With so many reporting and analytics tools at your disposal, virtual reality programming languages you can paint a clear picture of what’s working and what’s not. This way you can plug the gaps in your support and keep improving your customer experience. Access critical insights to improve your overall support metrics with Freshdesk-GoodData Integration.
The HubSpot Customer Platform
Instead, he encourages them to picture and achieve a goal of seamless delivery of value. But, the biggest driver of moving the operation from point A to point B is knowing what point B is,” Duggan explains. At the risk of stating the obvious, remember that the focus of operational excellence is operations. This approach does not deal with strategy, such as decisions about which products to offer, how to distribute them, or which geographic markets to enter.
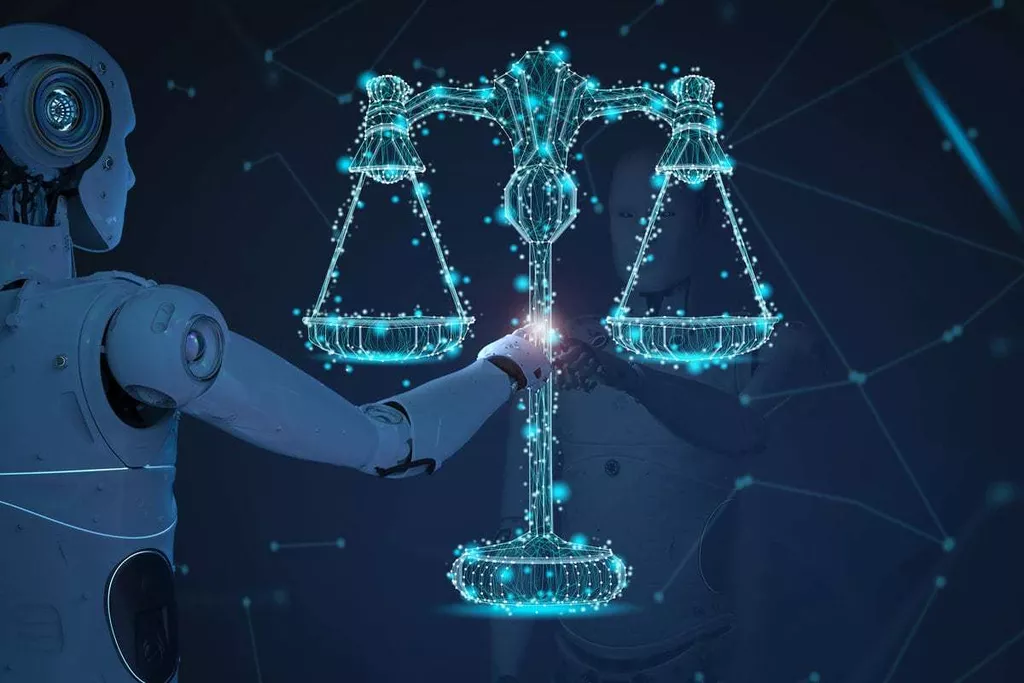
The key principles of lean manufacturing focus on improving the quality of products and services, eliminating anything that doesn’t add value, and reducing overall costs. For example, if you’d like to enhance the customer experience with a more knowledgeable workforce, set a goal for the amount of training employees should go through to understand the products and services better. Finally, people-oriented goals concentrate on workforce and cultural efforts that play a critical role in making an organization operationally excellent. Examples include growing employee engagement in operational excellence efforts, increasing skill training, and maximizing employee productivity.
Principle #5: Focus on the Process
It requires investing in service capacity ahead of the current requirements in order to be able to treat each moment of truth with the quality that the customer intrinsically needs or wants. The Complexity Line Model is based on the work of Bob Bergin and Gerri Prusko at Hanover Insurance Co. (Worcester, MA). The author has developed and used a Service Quality Management computer simulator to provide practice fields for managers to understand the complexity line concepts. Kim, MIT Organizational Learning Center, MO-294, 1 Amherst St., Cambridge, MA 02139.

The result is that many of today's manufacturing processes are burdensome and costly rather than being sources of value. Until this cost distortion is acknowledged and corrected, major management decision systems, including long-term strategy formulation, remain extremely difficult to validate. Accepting such a reality has been impossible for many of our finest executives.
The Importance of Continuous Improvement in Lean and Agile
As manufacturers worldwide grapple with market volatility, achieving and maintaining this level of excellence offers a significant competitive edge. It drives productivity, enhances customer satisfaction, and ultimately, improves bottom-line results. To truly reach a standard of service excellence you have to give your customer service team the freedom to do whatever it takes for final resolution -whether that’s making compromises or spending a little extra. One such example of this approach to customer service was demonstrated by Ritz Carlton.
What Is Operational Excellence In Marketing?
This means that a large part of the successful companies can be explained by the configurations in the solution, but that there are still other ways to achieve performance. One explanation for the lower coverage results are the different industries in our sample as well as different market conditions, which are not covered in this model, as this would increase the complexity. Operational excellence has swept healthcare, and it’s not surprising because quality, value, and waste are top-of-mind concerns for policymakers and healthcare providers.
Experience iD
First, make sure to communicate the essential aspects of the program, such as the mission, goals, and KPIs, to those impacted.That way they have the full view of what your organization is trying to achieve. Then, provide an open feedback channel so employees, managers, and leaders can stay in close contact throughout the process. Kaizen is based on the idea that every process can be improved, no matter how efficient it may seem to be. The methodology involves a systematic approach to identifying and eliminating waste, reducing variability, and improving quality.